Services
Services
Bäckman Blästermaskiner AB and SBM have a full range of blast equipment - wherever you are in the decision-making process and whatever your needs are. Our expert staff are happy to provide the support you need to ensure a reliable solution. Thanks to our extensive experience of the entire production chain we can be an asset - whenever and wherever you need us – either as an independent partner in an initial phase, or by offering a turnkey production facility.
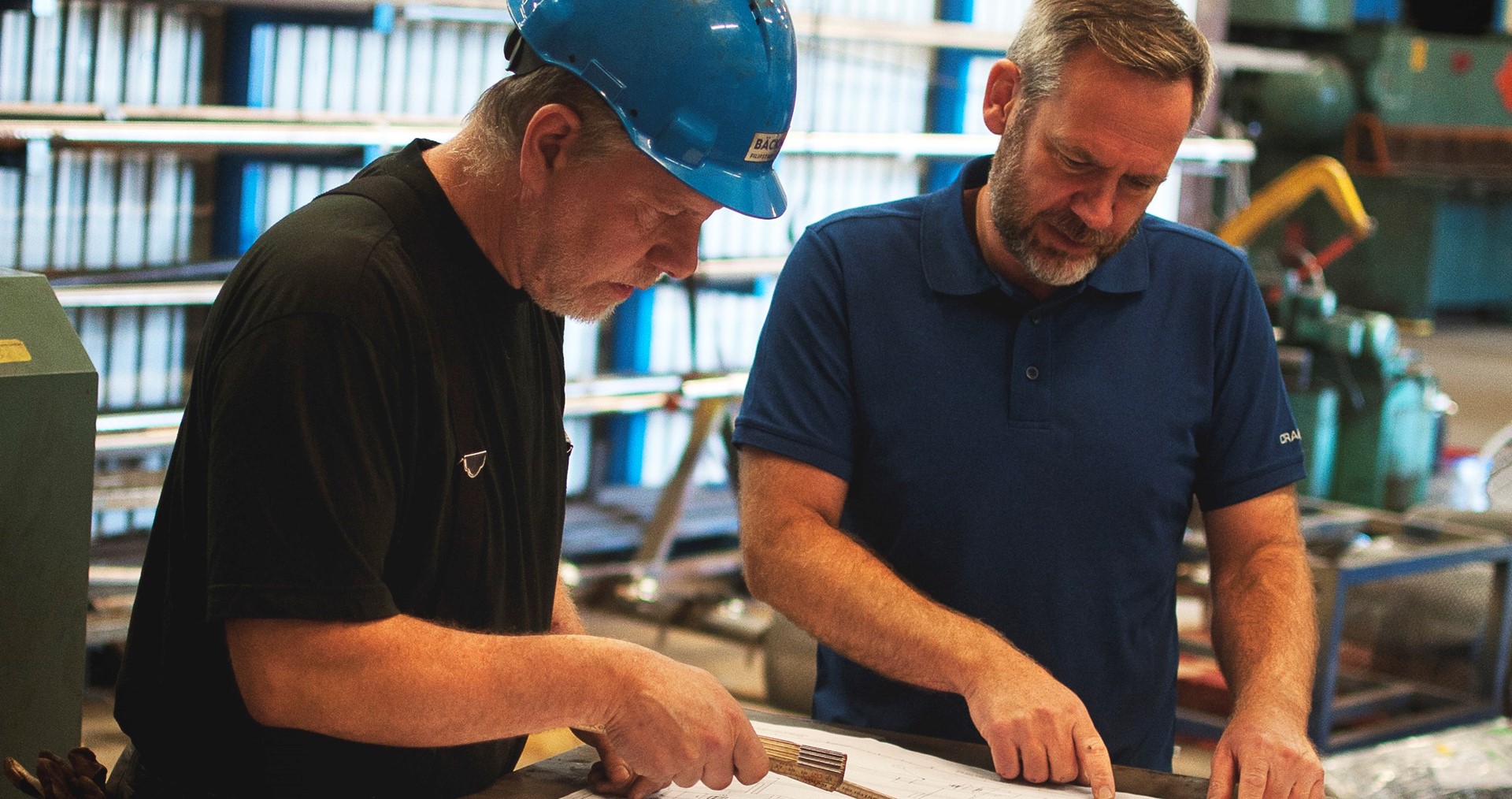
The aim of trial blasting is to evaluate the concept prior to investment in new equipment or the modification of existing machinery, while at the same time ensuring that results meet your expectations. These results are documented, and we guarantee corresponding results from the solution that we supply to you. Trial blasting is generally carried out in one of the hundreds of machines we have installed – or at our own workshop in Filipstad.
The environment and safety are areas that are subject to constant development, improvement and change. We keep ourselves up to date and continuously try to make our machines safer and more user and environmentally friendly – expertise we are happy to share. This knowledge transfer may take place in conjunction with a new investment, or when we play an active part in your environmental work on an existing installation. Naturally we comply with EU directives, but we also take account of your existing safety systems, modifying them where necessary. The environment around the machine is an important factor: If noise levels are unacceptable we can reduce them by constructing noise barriers, or review the materials handling process and suggest solutions. Other areas that can have a direct impact on the immediate environment are the handling of blast media and the correct design of filters and ventilation.
Our telephone support line is manned round the clock so as to minimise downtime. We can be on site in a matter of hours – wherever you are in the Nordic region.
Do you really need a new blast machine? This is a question we always ask before suggesting a solution. We have carried out many upgrades, everything from minor modifications to extensive refurbishment – all so that our customers are able to meet future requirements. We are leaders in the development of our field and can offer you the very latest technology to improve and simplify your existing blasting process. Together we can find the best solution. Contact us to set up an introductory meeting with our experienced technicians.
There are generally many questions to be answered before making a decision to invest or make changes. Will making efficiencies live up to our expectations? Which method will provide us most benefit? What will the cost structure be, initially and ongoing? Can we fit the blasting process into the flows and physical space of our existing environment?
To clear up any uncertainty we generally recommend some form of preliminary study. This provides an objective basis for assessing feasibility and choosing an approach based on your unique production environment.
For us, manufacturing or modifying a machine is all about a natural partnership between the customer and our staff - staff who have extensive experience of service, design and fabrication. If you have a basic plan or idea as to how you would like to make an improvement, our technicians will help to realise this project.
We install and commission new installations – as well as refurbishing or moving existing machines. Before a machine is taken into operation we test it, adjust it, fine tune it and train your staff. Training takes place for operators and also for service and maintenance staff.
With 50 years of experience of blast machines we are well aware that no chain is stronger than its weakest link. This is why we are proud, not only to be able to talk about our unique service and the genuine commitment we have to our customers, but also to be able to demonstrate it with our high levels of service. We stock spare parts for all machines, throughout their service life, and carry out regular maintenance based on the machine's utilisation. Our emergency support service is never closed. And our service agreements are guaranteed to provide all the security you could need.